The Facts About Lean Production Revealeds
Wiki Article
Fascination About Oem
Table of ContentsOem for DummiesMore About Additive ManufacturingEverything about Manufacturing IndustriesThe Ultimate Guide To Lean ManufacturingThe Only Guide for MfgIndicators on Hon Hai Precision You Need To Know
The text on this page is a sample from our full White Paper 'Injection Moulding for Buyers' - * Sample text * - for full overview click the download switch over! Intro This overview is meant for individuals that are looking to source plastic mouldings. It provides a much required understanding right into all that is entailed with producing plastic components, from the mould tool needed to the moulding process itself.If you intend to discover even more, the guide covers sorts of mould tools, along with unique completing procedures such as colours & plating. Words that are underscored can be located in the reference in the appendix ... Part I: Moulding: The Basics The Benefits of Injection Moulding Plastic shot moulding is an extremely accurate process that supplies a number of advantages over various other plastic handling techniques.
Precision is excellent for extremely elaborate parts. Compared to various other techniques, moulding enables you to include even more features at really little resistances. Have a look at the photo to the. You can hold this moulding in the palm of your hand as well as it has bosses, ribs, steel inserts, side cores and openings, made with a gliding shut down feature in the mould device.
Excitement About Lean Production
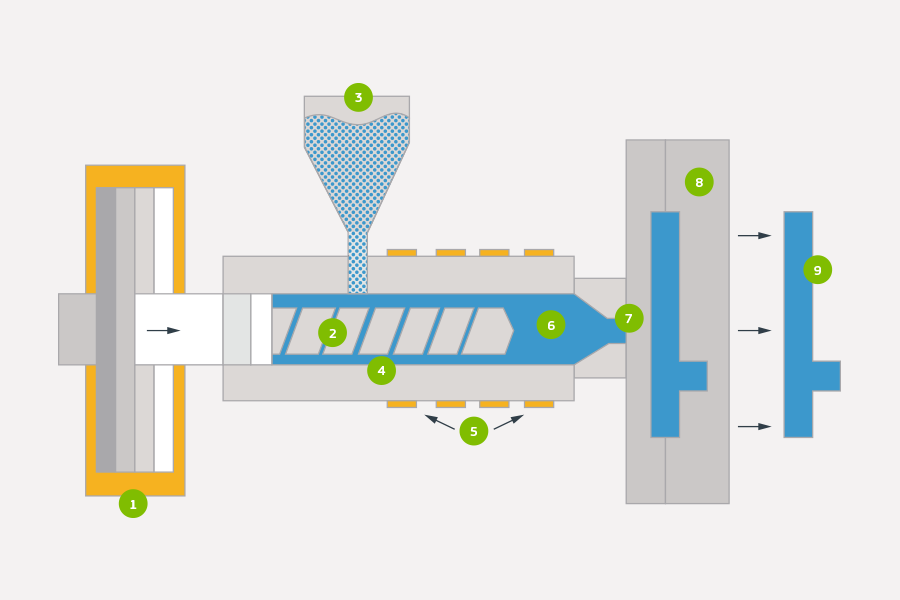

from material feed & melting; product shot; cooling time and also ejection to the re-closing of the mould device prepared for the following cycle. Draft angles - The wall surfaces of a moulded part ought to be a little tapered in the direction in which the part is expelled from the mould device, to allow the component to be expelled easily.
Ejector stroke - The pushing out of ejector pins to expel the moulded part from the mould tool. Ejector stroke rate, length and timing requires to be very carefully managed to stop damages to the ejectors as well as mould tool, however at the same time make the moulding cycle as brief as possible.
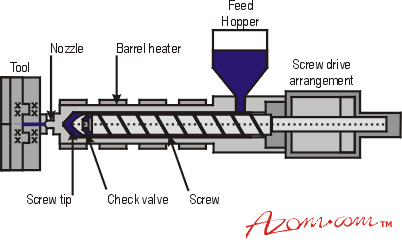
The Buzz on Hon Hai Precision
Ribs - When a plastic component has thin walls, ribs are included in the layout to make the slim walls stronger Side cores - Side activity which generates an attribute on a moulded part, at an opposing angle to the like it normal opening instructions of the mould device. lean manufacturing. The side core needs to be able to withdraw as the plastic component can not be ejected or else.
Wall surfaces - The sides of a moulded component The text on this page is a sample from our complete White Paper 'Injection Moulding for Purchasers'.
Shot moulding is widely used for making a variety of parts, from the tiniest elements to whole body panels of autos. Developments in 3D printing technology, making use of photopolymers that do not melt during the shot moulding of some lower-temperature thermoplastics, can be used for some basic injection moulds. Injection moulding utilizes a special-purpose machine that has three components: the injection unit, the mould and also the clamp.
The Definitive Guide to Lean Manufacturing
Process qualities [edit] Shot moulding uses a ram or screw-type bettor to compel molten plastic or rubber material right into a helpful resources mould tooth cavity; this solidifies right into a form that has satisfied the shape of the mould. It is most typically used to refine both thermoplastic and thermosetting polymers, with the quantity used of the former being considerably higher.: 13 Thermoplastics are widespread because of characteristics that make them highly ideal for injection moulding, such as ease of recycling, convenience for a variety of applications,: 89 and capability to soften and move on home heating.In several cavity moulds, each tooth cavity can be the same as well as create the same components or can be special and also create several different geometries during a solitary cycle. Moulds are typically made from device steels, but stainless steels and also aluminium moulds appropriate for sure applications. Aluminium moulds are normally improper for high volume production or get rid of slim dimensional tolerances, as they have substandard mechanical homes as well as are extra prone to use, damages, and also deformation during the injection as well as securing cycles; nonetheless, aluminium moulds are economical in low-volume applications, as mould fabrication expenses and also time are substantially reduced.
When sufficient material has gathered, the material is required at high stress and velocity right into the part developing cavity. The exact quantity of shrinking is a function of the material being made use of, and can be fairly predictable. To avoid spikes in stress, the procedure normally makes use of a transfer position representing a 9598% full cavity where the screw changes from a continuous speed to a constant pressure control.
Some Known Questions About Manufacturing Industries.
The packaging pressure is applied up until the entrance (tooth cavity entryway) solidifies. Due to its little size, the gate is normally the first place global foundry to strengthen with its entire thickness.: 16 Once the entrance solidifies, no even more material can enter the tooth cavity; appropriately, the screw reciprocates as well as obtains material for the next cycle while the material within the mould cools so that it can be expelled and be dimensionally stable.Report this wiki page